Case Study:
AI-Optimized Office Building Saves 40% in Materials
Discover how advanced AI algorithms revolutionized the design of a cutting-edge office complex, slashing material usage while enhancing structural integrity and sustainability.
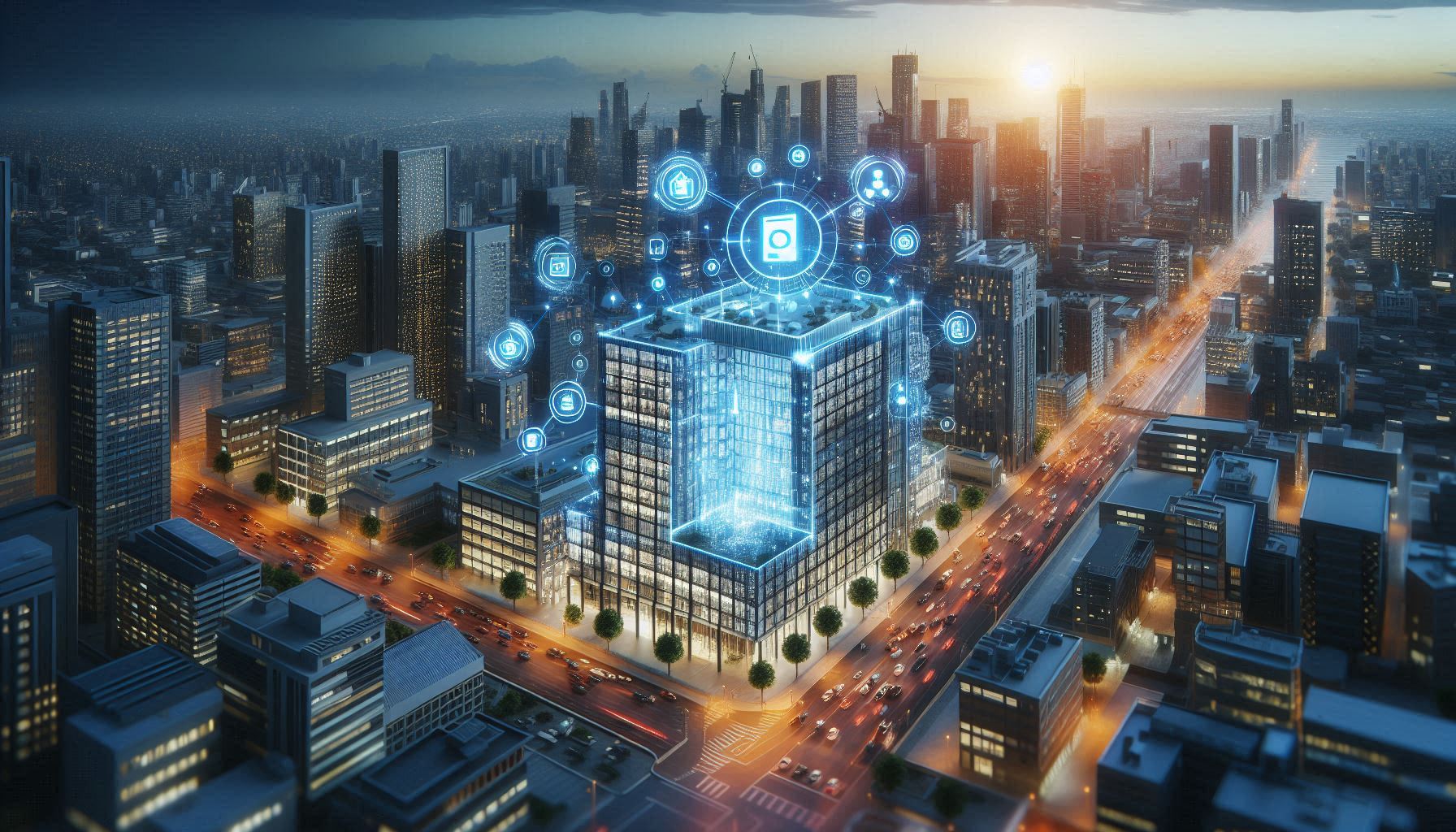
Traditional Building Design Challenges
Before exploring our AI-optimized solution, it's important to understand the inherent inefficiencies in conventional structural design approaches:
Material overuse
- •Traditional structural design methods often lead to excessive material usage due to conservative safety factors and standardized approaches.
Design constraints
- •Complex architectural visions are frequently compromised due to structural limitations and inability to rapidly simulate multiple alternatives.
Environmental impact
- •Construction materials account for approximately 11% of global carbon emissions, with steel and concrete production being particularly carbon-intensive.
Integration complexity
- •Balancing structural requirements with MEP systems, sustainability features, and spatial needs typically requires lengthy, iterative processes.
Project Overview: The SustainaHub Tower
When TechVision Enterprises approached us with their ambitious plan for a new 30-story headquarters in downtown Seattle, their requirements were challenging: create an iconic, sustainable structure that would reduce environmental impact without compromising on architectural vision or functionality.
The traditional approach would have required significant material redundancy to accommodate the building's unique curved form and cantilevered upper floors. Early estimates suggested over 12,000 tons of structural steel would be needed—a figure that would substantially impact both the project budget and carbon footprint.
Instead, our team proposed leveraging our new AI-powered structural optimization platform, StructAI, to find a solution that would maintain the architectural vision while dramatically reducing material requirements.
The AI-Driven Design Process
Phase 1: Parameter Definition and Constraints
The first step involved defining the project's core parameters and constraints. Rather than starting with a predetermined structural system, we input the architectural vision, spatial requirements, local building codes, seismic considerations, and desired sustainability metrics into the StructAI platform.
The system also incorporated site-specific data, including:
- Soil composition and foundation requirements
- Wind load patterns specific to the downtown Seattle location
- Solar exposure throughout the year
- Adjacent building influences
- Local material availability and supply chain considerations
Unlike traditional approaches where constraints often limit possibilities, our AI system used these parameters as the foundation for exploring thousands of potential solutions.
Phase 2: Generative Design Exploration
With the parameters established, StructAI generated over 10,000 possible structural configurations in just 72 hours—a process that would have taken a conventional team months to complete. Each design was evaluated against multiple criteria:
- Structural integrity and safety (with appropriate safety factors)
- Material efficiency and optimization
- Construction feasibility and timeline impact
- Cost implications
- Carbon footprint and environmental impact
- Aesthetic alignment with architectural vision
- Spatial optimization and usability
The platform didn't just analyze each configuration individually—it learned from each iteration, progressively refining its approach to generate increasingly efficient solutions.
Phase 3: Collaborative Refinement
While AI drove the computational aspects, human expertise remained essential. Our structural engineers worked closely with TechVision's architects through an interactive interface that allowed real-time collaboration on the evolving design.
This hybrid approach allowed the team to make informed decisions about trade-offs between different priorities. When architects suggested modifications to enhance certain spaces, the AI instantly recalculated structural implications and proposed alternative solutions that maintained efficiency.
This collaborative process continued through several cycles of refinement until the team arrived at an optimal design that satisfied all stakeholders.
Results: 40% Material Reduction Without Compromise
The final design achieved remarkable results:
- 40% reduction in structural steel compared to conventional design approaches (from an estimated 12,000 tons to just 7,200 tons)
- 35% reduction in concrete volume for foundations and core elements
- 28% decrease in overall embodied carbon compared to baseline estimates
- Full compliance with all structural codes and safety requirements, with appropriate safety factors
- Preservation of 100% of the original architectural vision and spatial requirements
- 15% reduction in construction time due to optimized assembly sequences and reduced material handling
Perhaps most impressively, these gains came without any increase in construction costs. While the AI-driven design process represented an additional upfront investment, this was more than offset by the material savings and reduced construction timeline.
Key Innovations in the Final Design
Several specific innovations contributed to these impressive results:
1. Topology-Optimized Floor Systems
The AI identified opportunities to create variable-depth floor systems that concentrated material precisely where loads were highest. This approach eliminated unnecessary material while maintaining required stiffness and vibration characteristics.
2. Adaptive Column Grid
Rather than using a uniform column grid throughout the building, the system developed a variable grid that responded to changing loads and spatial requirements at different levels. This created more open, column-free spaces in public areas while maintaining structural efficiency.
3. Integrated Facade Support System
The structural system was fully integrated with the curtain wall support requirements, eliminating redundant elements and reducing connection complexity. This not only saved material but also simplified construction and improved thermal performance by reducing thermal bridges.
4. Site-Specific Foundation Design
By analyzing detailed geotechnical data, the AI optimized foundation elements specifically for the site's soil conditions, resulting in a 35% reduction in concrete and reinforcement without compromising stability.
Implementation Challenges and Solutions
Despite the clear benefits, implementing such an innovative structural approach wasn't without challenges:
Challenge 1: Construction Team Adaptation
The optimized design departed from conventional construction methods, requiring specialized training for the construction team. We addressed this by:
- Creating detailed 3D visualizations and assembly sequences
- Developing simplified connection details that reduced complexity in the field
- Implementing AR-based guidance systems for critical assembly operations
- Conducting training sessions with key subcontractors before construction began
Challenge 2: Regulatory Approval
The novel approach required additional documentation and verification for building officials. Our solution included:
- Comprehensive structural calculations and third-party verification
- Physical testing of critical connection details
- Progressive load testing during construction to validate performance
- Ongoing monitoring systems to verify actual behavior matched predictions
Challenge 3: Supply Chain Coordination
The optimized design required precise material specifications and just-in-time delivery. We implemented:
- Digital twin integration with fabricator systems for seamless data transfer
- AI-optimized fabrication and delivery sequencing
- Real-time tracking of all major structural components
- Prefabrication strategies for complex assemblies to reduce field work
Long-Term Impact and Performance Monitoring
The SustainaHub Tower isn't just designed differently—it's also built to learn and improve over time. The building incorporates:
- Embedded sensor network monitoring actual structural behavior and comparing it to predicted performance
- Real-time data analysis that will inform future design optimization
- Ongoing digital twin that tracks building performance across multiple metrics
- Material provenance tracking to verify the actual embodied carbon throughout the supply chain
This information feeds back into our AI platform, continuously improving its algorithms and predictions for future projects. The building essentially becomes a living laboratory for structural innovation.
Early monitoring results (6 months post-occupancy) confirm that the structure is performing as predicted, with deflections and vibration characteristics well within design parameters. Energy performance is exceeding expectations, with the optimized structure contributing to improved thermal performance.
Broader Implications for the Construction Industry
The success of the SustainaHub Tower demonstrates that AI-driven structural optimization isn't just a theoretical concept but a practical approach that delivers tangible benefits:
-
Environmental Impact: If similar approaches were applied across the commercial building sector, we estimate potential reductions of 100+ million tons of CO2 emissions annually.
-
Economic Benefits: The material efficiency gains translate directly to cost savings, making sustainable construction more economically viable.
-
Architectural Freedom: By finding structural solutions that might not be obvious to human engineers, AI opens new possibilities for architectural expression.
-
Industry Transformation: The process represents a fundamental shift from intuition-based to data-driven design approaches.
-
Skills Evolution: Rather than replacing structural engineers, AI is elevating their role to focus on creative problem-solving and design leadership.
The SustainaHub Tower has already influenced local building codes, with officials now considering incentives for projects that demonstrate similar material efficiency gains.
Conclusion: A New Standard for Structural Innovation
The SustainaHub Tower case study demonstrates that the 40% reduction in structural materials isn't just an impressive statistic—it represents a fundamental rethinking of how we approach building design and construction.
By harnessing AI not as a replacement for human expertise but as a powerful tool to extend our capabilities, we've shown that it's possible to simultaneously reduce environmental impact, control costs, and enhance architectural possibilities.
As we continue to refine our approach and apply these techniques to new projects, we expect to push the boundaries even further. The next generation of AI-optimized buildings may achieve 50-60% material reductions while introducing entirely new structural forms and functions.
The future of structural engineering isn't about choosing between efficiency and expression—it's about using advanced technology to deliver both simultaneously. The SustainaHub Tower isn't just a building; it's a blueprint for a more sustainable, innovative approach to the built environment.
Written by
StructAI Research Team
A collaborative team of structural engineers and AI specialists.
Want to reduce materials in your next project?
Our AI-powered structural optimization platform can help you achieve similar material savings while enhancing performance. Whether you're planning a small commercial building or a major development, our technology scales to meet your needs.
Currently working with projects over 50,000 square feet. Early access program available for smaller projects.
Related Case Studies
AI-Optimized Bridge Design Reduces Carbon Footprint by 35%
March 22, 2025 • 5 min read
How generative design transformed a challenging river crossing project.
Multi-Parameter Optimization for Hospital Design Improves Patient Outcomes
April 5, 2025 • 7 min read
Balancing structural efficiency with healthcare-specific requirements.