Transforming Construction with
Generative AI and Digital Twins
Discover how the convergence of generative AI and digital twin technology is revolutionizing the construction industry with smarter designs, reduced waste, and enhanced project lifecycle management.
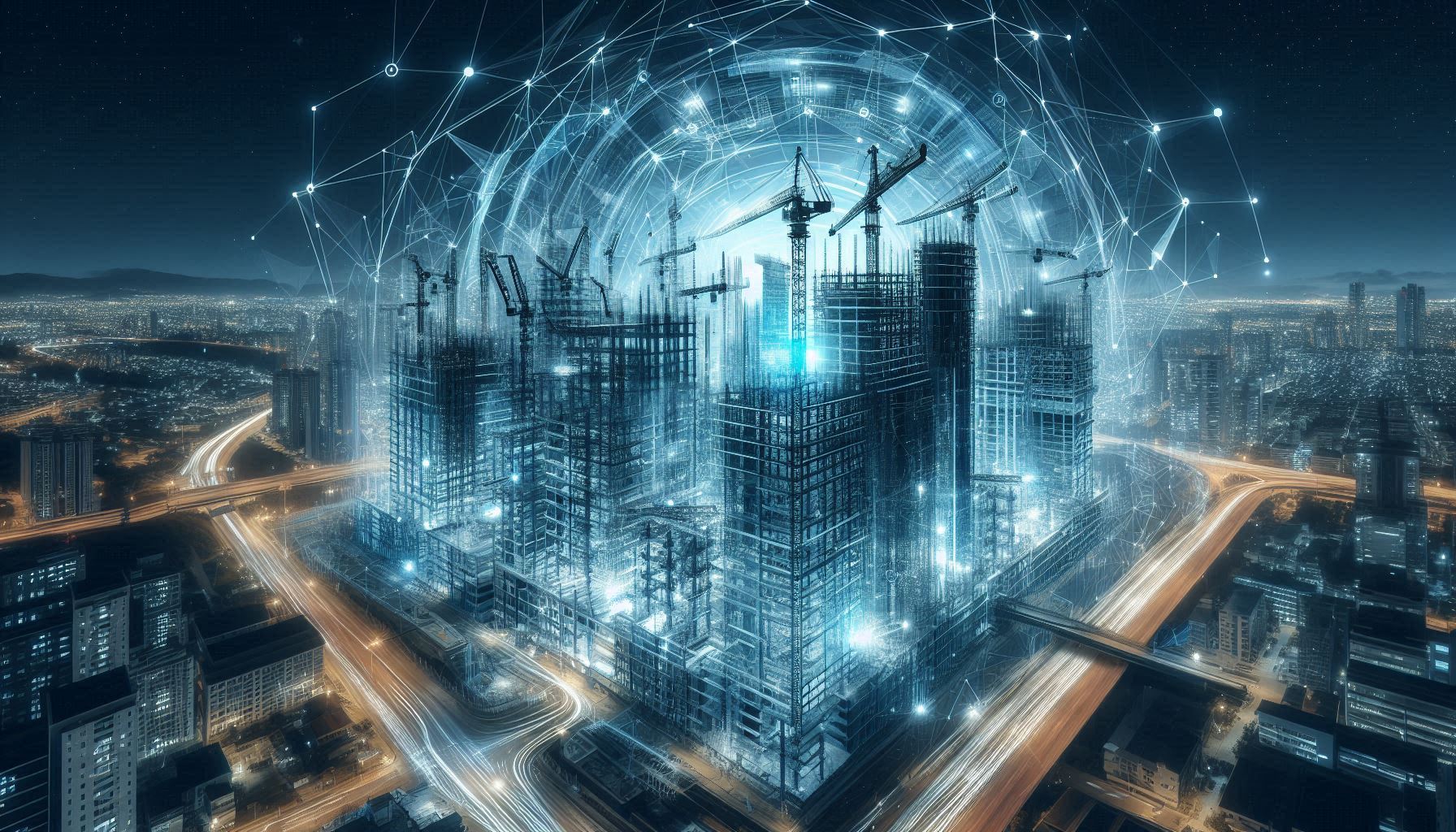
Key Construction Industry Challenges
Before exploring how AI and digital twins are transforming construction, it's essential to understand the fundamental challenges these technologies address:
Fragmented workflows
- •Traditional construction processes involve multiple disconnected tools and stakeholders, leading to information silos and coordination challenges.
Inefficient resource use
- •The construction industry accounts for nearly 40% of global CO2 emissions and generates massive waste due to overengineering and rework.
Risk management
- •Construction projects frequently experience delays and cost overruns due to unforeseen complications that could be identified earlier with better prediction tools.
Performance optimization
- •Buildings often underperform in energy efficiency, spatial functionality, and lifecycle cost due to limited design exploration and optimization capabilities.
The Convergence of Two Transformative Technologies
The construction industry stands at the cusp of a technological revolution driven by two complementary innovations: generative AI and digital twins. While each technology offers significant benefits independently, their integration creates a powerful synergy that promises to fundamentally transform how buildings are designed, constructed, and operated.
Understanding Generative AI in Construction
Generative AI refers to algorithms that can create novel designs and solutions based on specified parameters and constraints. Unlike traditional CAD systems that merely execute explicit human instructions, generative AI actively participates in the creative process by:
- Exploring thousands of design possibilities beyond human cognitive limitations
- Optimizing for multiple competing objectives simultaneously (structural efficiency, energy performance, cost, etc.)
- Learning from previous designs and continuously improving its output
- Adapting solutions to specific site conditions, regulations, and client requirements
Recent advances in deep learning and computational capabilities have dramatically enhanced these systems' sophistication, allowing them to move from theoretical applications to practical tools used in real-world projects.
Digital Twins: Beyond 3D Models
While 3D modeling has been used in construction for decades, digital twins represent a quantum leap forward. A digital twin is not merely a static representation but a dynamic, data-rich virtual replica that:
- Maintains a real-time connection with its physical counterpart
- Incorporates IoT sensor data to reflect actual performance
- Serves as a comprehensive information repository across the entire building lifecycle
- Enables simulation and prediction of future behaviors and scenarios
As BIM (Building Information Modeling) evolves into true digital twin capability, it creates the perfect foundation for generative AI to work with rich, contextualized data about both design intent and operational reality.
How This Technological Convergence Transforms Construction
Design Phase Revolution
The traditional design process often involves limited exploration of alternatives due to time and resource constraints. Generative AI radically expands this creative space:
-
Design Exploration: Architects and engineers can evaluate thousands of design options that meet functional requirements while optimizing for parameters like material usage, energy performance, and constructability.
-
Multi-objective Optimization: Rather than simplistic cost-based decisions, projects can balance complex factors like embodied carbon, operational energy use, occupant comfort, and lifecycle costs simultaneously.
-
Constraint Satisfaction: AI systems can navigate the complex web of building codes, zoning regulations, and accessibility requirements, automatically ensuring compliant designs.
-
Form Finding: Generative algorithms can discover novel structural forms that minimize material use while maintaining or enhancing performance, leading to buildings that are both more efficient and architecturally distinctive.
A digital twin serves as both the input source for these algorithms and the platform where stakeholders can evaluate and refine the AI-generated options.
Construction Phase Transformation
The benefits extend well beyond design into the construction process itself:
-
Constructability Analysis: AI can identify potential conflicts and assembly challenges before breaking ground, drastically reducing costly field changes.
-
Supply Chain Optimization: Generative algorithms can optimize material ordering, fabrication sequencing, and logistics to minimize waste and delays.
-
Automated Progress Monitoring: By comparing real-time site conditions (captured via drones, lidar, or other technologies) with the digital twin, the system can automatically track progress and identify deviations.
-
Safety Enhancement: AI analysis of construction sequences within the digital twin can identify potential safety hazards before they cause incidents on site.
-
Resource Allocation: Predictive algorithms can optimize crew assignments and equipment utilization based on continuously updated project status.
Operational Excellence Through Digital Twin Intelligence
Once construction is complete, the digital twin continues to deliver value throughout the building's operational life:
-
Predictive Maintenance: By analyzing patterns in sensor data against expected performance parameters, AI can predict equipment failures before they occur, enabling proactive maintenance.
-
Energy Optimization: Generative algorithms can continuously fine-tune building systems based on actual usage patterns, weather conditions, and energy costs.
-
Space Utilization: Occupancy data integrated into the digital twin allows AI to recommend spatial reconfigurations that better serve evolving usage needs.
-
Resilience Planning: Simulation capabilities enable testing building responses to extreme events like power outages, natural disasters, or pandemic-driven occupancy changes.
-
Lifecycle Cost Management: The combination of actual performance data and predictive capabilities allows for more accurate lifecycle cost assessment and value engineering.
The digital twin becomes a living document that grows richer over time, with each operational insight feeding back into the AI systems to improve future designs in a virtuous cycle of continuous improvement.
Case Study: The Nexus Tower Project
To illustrate these concepts in action, consider the Nexus Tower, a 42-story mixed-use development completed in 2024 that leveraged the integrated generative AI and digital twin approach throughout its lifecycle.
Design Phase Implementation
The project began with a comprehensive set of parameters:
- Site constraints and zoning envelope
- Program requirements for office, residential, and retail spaces
- Target budget and schedule
- Sustainability goals (LEED Platinum certification)
- Structural and systems performance requirements
Rather than proceeding with a single design concept, the architectural team used generative AI to explore over 5,000 possible configurations within these constraints. The system evaluated each option against multiple criteria:
- Structural efficiency and material usage
- Solar exposure and potential energy generation
- Wind loads and aerodynamic performance
- Views and natural light for occupant spaces
- Spatial efficiency and program relationships
- Construction sequencing and logistics
The selected design achieved:
- 32% reduction in structural steel compared to conventional approaches
- 28% improvement in energy performance compared to baseline
- 15% increase in rentable floor area within the same building envelope
- Optimal placement of mechanical systems to reduce distribution losses
Throughout this process, the evolving digital twin allowed stakeholders to experience proposed designs through VR, evaluate performance data, and provide feedback that informed subsequent design iterations.
Construction Execution and Monitoring
During construction, the Nexus Tower digital twin became the central coordination hub:
-
Precise Fabrication: Structural components were directly manufactured from the digital twin model, with tolerances of less than 2mm, drastically reducing field adjustments.
-
4D Scheduling: Construction sequences were simulated and optimized within the digital twin, with AI identifying critical path improvements that shortened the schedule by 3.5 months.
-
Automated Progress Tracking: Weekly drone surveys and laser scans were automatically compared to the digital twin to verify construction progress and dimensional accuracy.
-
Supply Chain Integration: Material deliveries were synchronized with construction progress, reducing on-site storage requirements by 65% compared to typical projects.
-
Quality Assurance: The digital twin served as the "single source of truth" for all quality checks, with field teams using augmented reality to compare as-built conditions to design intent in real time.
These innovations resulted in the project completing 8% under budget and 11% ahead of schedule—remarkable achievements for a project of this complexity.
Operational Intelligence and Building Performance
Since its completion, the Nexus Tower's digital twin has continued to evolve:
-
Sensor Network: Over 15,000 IoT sensors monitor everything from structural movement to air quality, with data continuously feeding into the digital twin.
-
AI-Powered Building Management: Rather than fixed schedules, the building's systems are dynamically optimized by AI algorithms that learn from usage patterns and environmental conditions.
-
Predictive Analytics: The system has successfully predicted and prevented six potential major equipment failures by identifying subtle performance deviations.
-
Space Optimization: When post-pandemic work patterns changed occupancy needs, the AI suggested spatial reconfigurations that improved utilization by 24%.
-
Continuous Commissioning: Rather than periodic recommissioning, the building's systems are continuously monitored and optimized, maintaining peak efficiency.
First-year results show the building is performing 7% better than even its advanced design projections for energy efficiency, with tenant satisfaction scores in the 93rd percentile for comparable properties.
The Future: Self-Improving Buildings and Portfolios
The Nexus Tower represents just the beginning of what's possible with the integration of generative AI and digital twins. As these technologies continue to mature, we can expect:
Self-Improving Building Designs
As digital twins capture more operational data across multiple buildings, generative AI will identify patterns and opportunities that lead to better designs:
-
Cross-Portfolio Learning: AI will identify which design strategies actually deliver the best performance across different building types, climates, and usage patterns.
-
Automated Design Generation: Future buildings will start with AI-generated baseline designs that incorporate all lessons learned from previous projects.
-
Continuous Optimization: Buildings will automatically adapt their operation based on actual usage patterns and changing conditions.
Enhanced Simulation Capabilities
The next generation of digital twins will simulate not just physical performance but also:
- Occupant Experience: Predicting how design choices will affect human comfort, productivity, and well-being
- Economic Performance: Modeling how building design influences rental rates, occupancy levels, and asset value
- Urban Integration: Simulating how buildings interact with surrounding infrastructure, transportation systems, and other buildings
Integrated Industry Transformation
The true transformation will come as these technologies extend beyond individual buildings to reshape the entire construction ecosystem:
-
Material Innovation: Generative AI will drive the development of new building materials optimized for specific performance characteristics and sustainability metrics.
-
Supply Chain Integration: Digital twins will extend to encompass the entire construction supply chain, optimizing everything from material production to assembly.
-
Circular Economy Enablement: Buildings will be designed from the outset with their eventual disassembly and material reuse in mind, with the digital twin maintaining the "material passport" throughout the lifecycle.
-
Regulatory Evolution: Building codes will evolve from prescriptive requirements to performance-based standards that can be simulated and verified within digital twins.
Implementation Challenges and Solutions
Despite their transformative potential, integrating generative AI and digital twins faces several challenges:
Data Quality and Standardization
AI systems require high-quality, structured data to function effectively. The construction industry's fragmented nature often results in inconsistent or incomplete information.
Solution: Industry initiatives like the Digital Twin Consortium and buildingSMART are developing standardized data protocols that enable seamless information exchange. Companies adopting these standards gain immediate advantages in data utilization.
Technical Expertise Gap
Many architecture, engineering, and construction firms lack the specialized skills needed to implement and leverage these advanced technologies.
Solution: Progressive firms are creating hybrid teams that pair domain experts with data scientists and AI specialists. Educational programs focused specifically on computational design and construction technology are emerging to address this gap.
Initial Investment Requirements
Implementing comprehensive digital twin platforms and AI capabilities requires significant upfront investment before ROI is realized.
Solution: Cloud-based SaaS solutions are making these technologies accessible at lower entry costs. Starting with targeted applications (e.g., energy optimization or structural design) can demonstrate value before scaling to comprehensive implementation.
Liability and Responsibility Questions
When AI systems generate designs or make operational decisions, questions arise about responsibility and liability for outcomes.
Solution: Emerging frameworks treat AI as a design assistant rather than an autonomous agent, with human professionals retaining review and approval authority. Insurance products specifically addressing technology-assisted design are being developed.
Getting Started: Strategic Implementation Roadmap
For organizations looking to leverage these technologies, we recommend a phased approach:
Phase 1: Foundation Building (3-6 months)
- Assess current data management practices and identify gaps
- Implement standardized data protocols across projects
- Train key team members on computational design principles
- Select initial use cases with clear ROI potential
Phase 2: Pilot Implementation (6-12 months)
- Deploy digital twin capabilities on a single project
- Implement targeted generative AI applications in specific domains (e.g., structural optimization)
- Establish metrics to measure impact and ROI
- Develop internal processes for AI-assisted design review and validation
Phase 3: Scaled Deployment (12-24 months)
- Expand digital twin implementation across project portfolio
- Integrate generative AI into standard workflows
- Develop feedback mechanisms to capture operational data for continuous improvement
- Create cross-functional teams to maximize technology utilization
Phase 4: Transformative Integration (24+ months)
- Implement portfolio-wide data integration and cross-project learning
- Develop proprietary AI algorithms tailored to organizational expertise
- Reimagine business models based on data-driven insights
- Lead industry transformation through innovation partnerships
Each organization's journey will vary based on existing capabilities, project types, and strategic objectives. However, delaying implementation risks competitive disadvantage as these technologies rapidly mature and reshape industry expectations.
Conclusion: The New Era of Data-Driven Construction
The convergence of generative AI and digital twins represents nothing less than a paradigm shift for the construction industry. After decades of lagging behind other sectors in productivity and technology adoption, construction now has the tools to address its most persistent challenges:
- Eliminating waste through optimized designs and precise execution
- Enhancing performance through data-driven decision making
- Improving sustainability by maximizing resource efficiency
- Accelerating delivery through streamlined processes and automation
- Extending lifecycle value through intelligent operations
The most successful organizations will be those that embrace these technologies not simply as new tools but as catalysts for reimagining how buildings are designed, delivered, and operated. The question is no longer whether these technologies will transform construction, but how quickly organizations will adapt to the new reality they create.
As we stand at this technological inflection point, one thing is clear: the buildings of tomorrow will not just be constructed—they will be computed, optimized, and continuously evolved through the powerful combination of human expertise and artificial intelligence, all orchestrated within their digital twins.
The future of construction has arrived, and it is intelligent, integrated, and data-driven.
Written by
Digital Construction Innovation Lab
A research team specializing in construction technology and computational design.
Ready to transform your construction workflow?
Our team of AI and digital twin specialists can help you implement these transformative technologies in your next project. Whether you're looking to optimize designs, streamline construction, or enhance building operations, we have solutions tailored to your needs.
Free assessment available for projects over $5M in construction value.